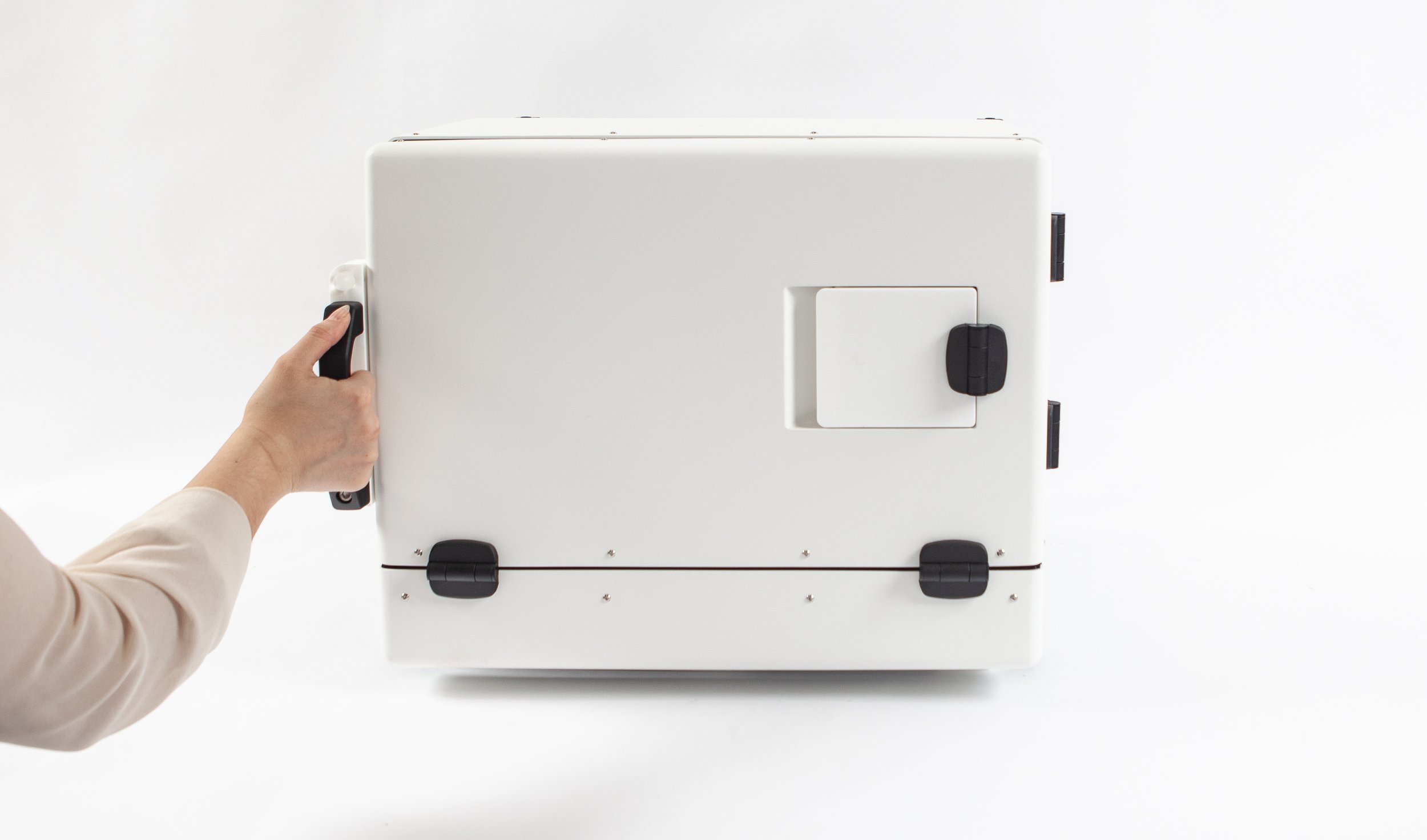
US20210340486A1
System and Method for Centralized
Fluid Management & Culture Control
As part of a collaborative engineering team, I contributed to the design of a centralized system for fluid management and culture control in bioreactors, specifically aimed at optimizing the growth of human cells, tissues, and tissue-based products. Our system automates the delivery of nutrient-rich media to multiple bioreactors while efficiently removing waste, all within a sterile environment that prevents cross-contamination. I helped integrate sensors to monitor critical fluid properties like temperature, pH, and gas concentrations, allowing the system to make real-time adjustments and maintain optimal growth conditions. The design features a centralized media reservoir that supplies fluid to each bioreactor, along with built-in fluid pumping and gas exchange mechanisms. By creating a controlled, scalable, and automated environment, our system significantly enhances the efficiency and consistency of tissue growth, making it ideal for advanced manufacturing applications in tissue engineering.
See a glimpse of the system in action at the 2:50 mark.
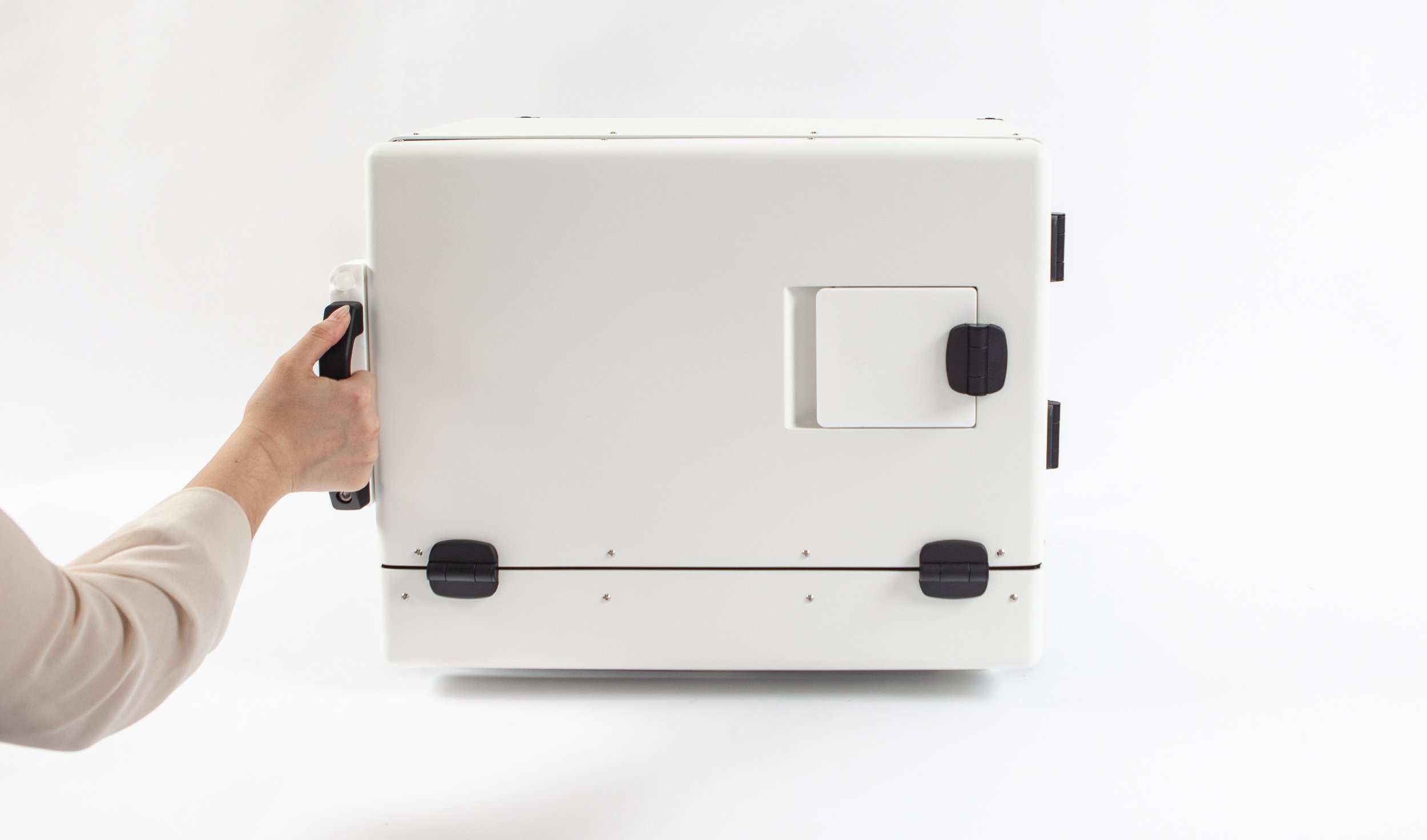
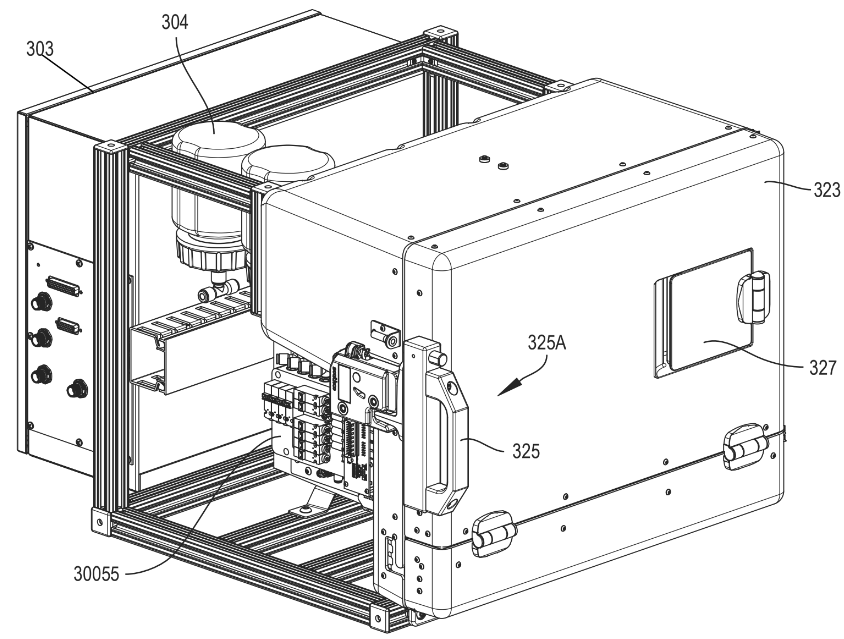
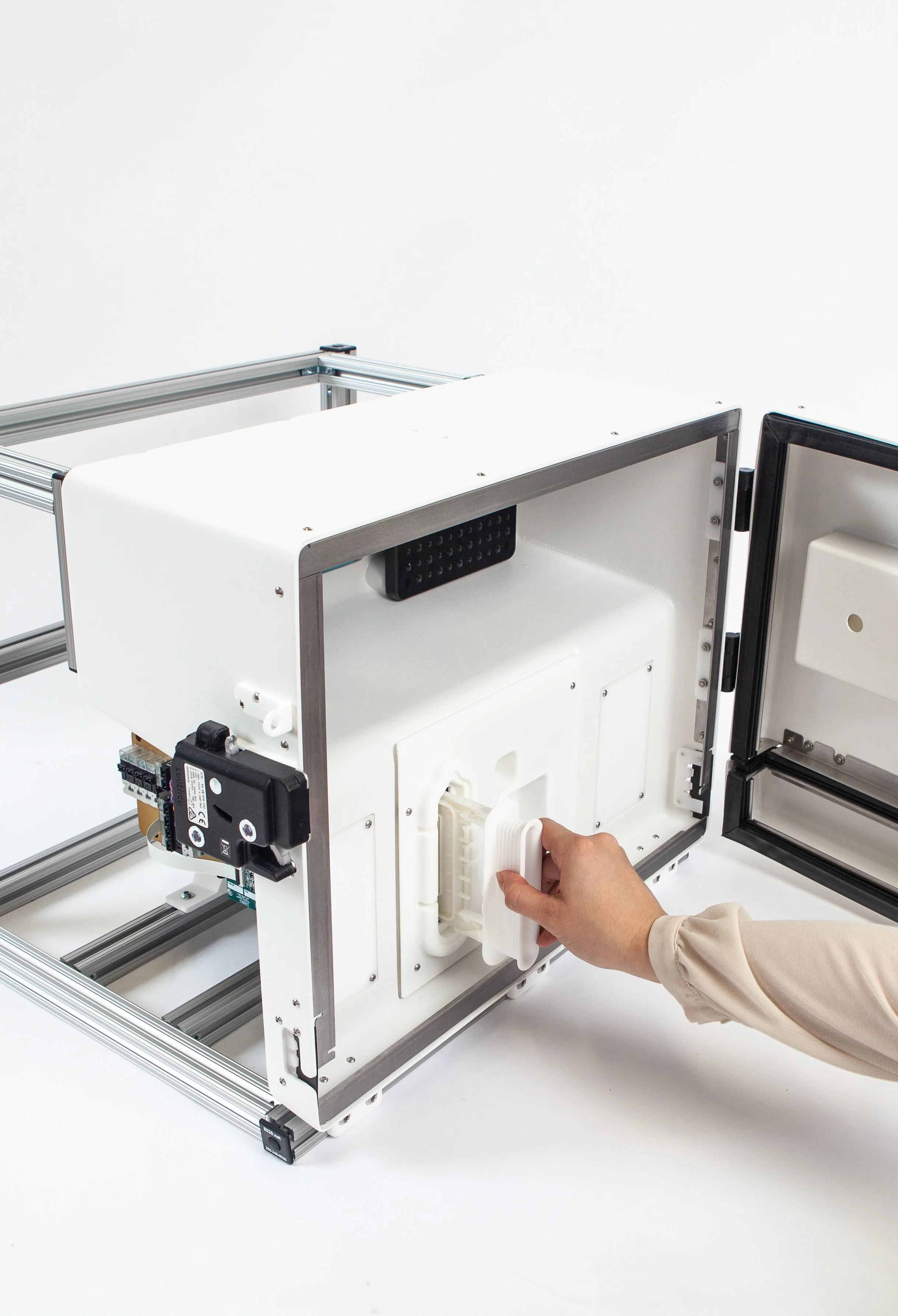

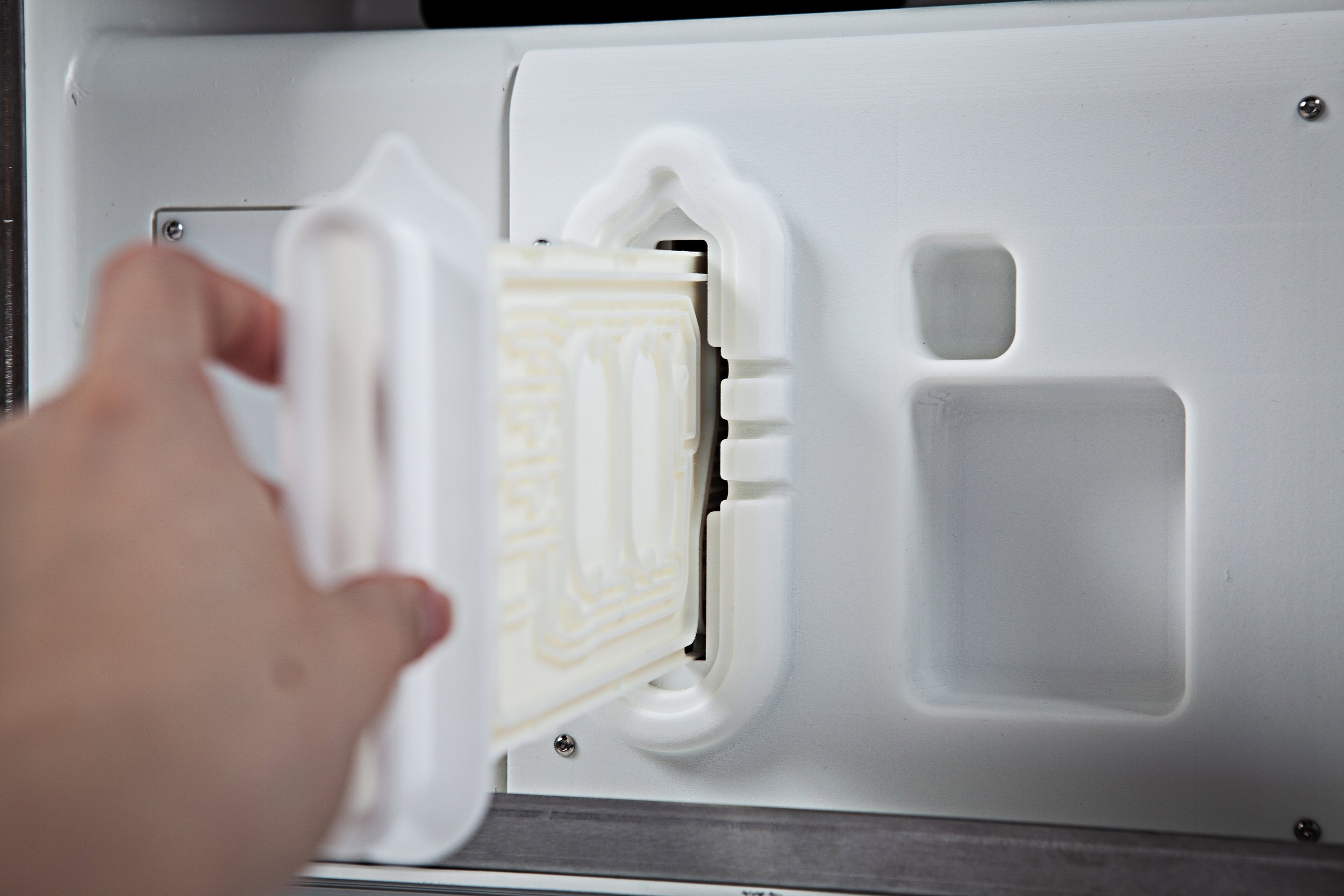

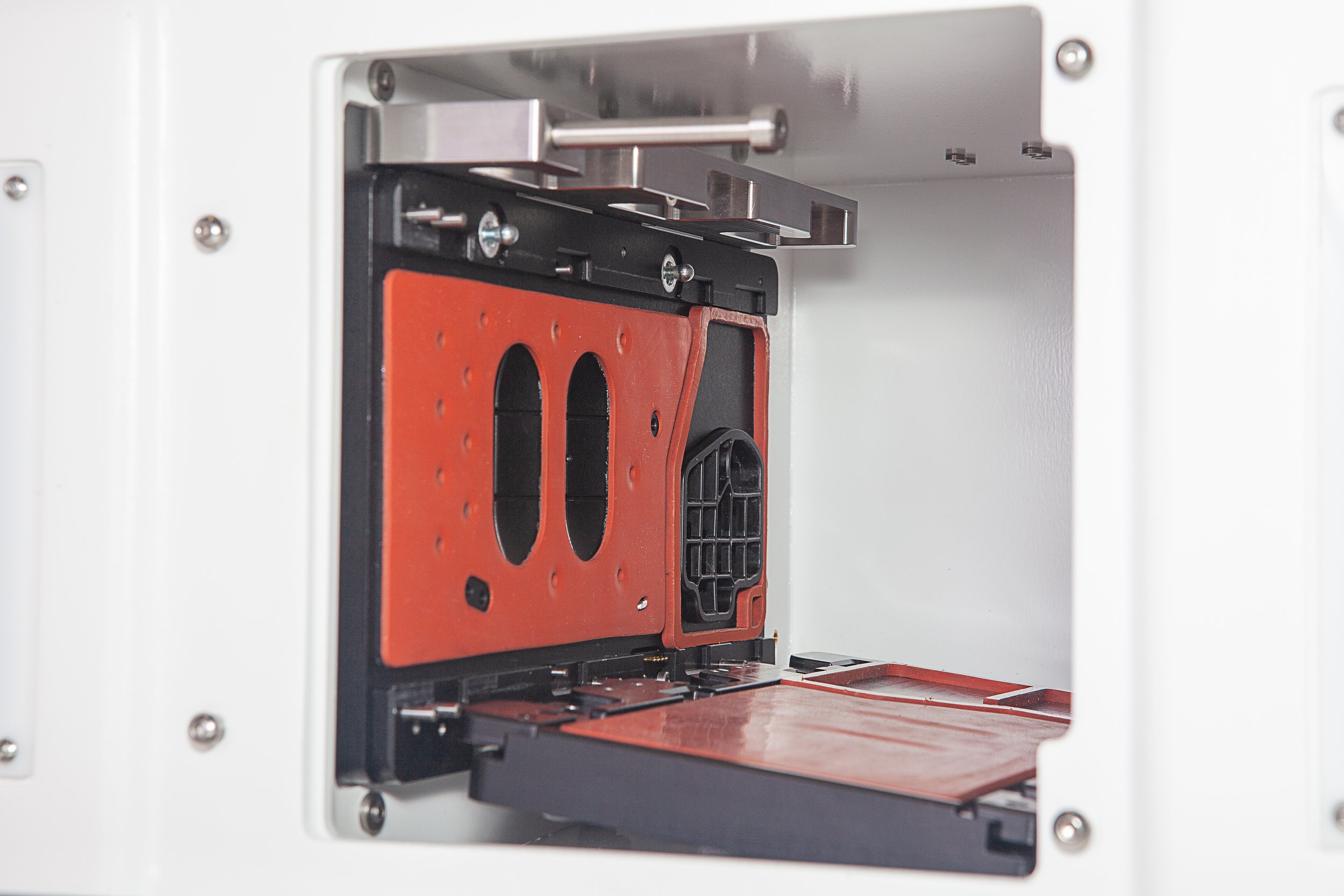

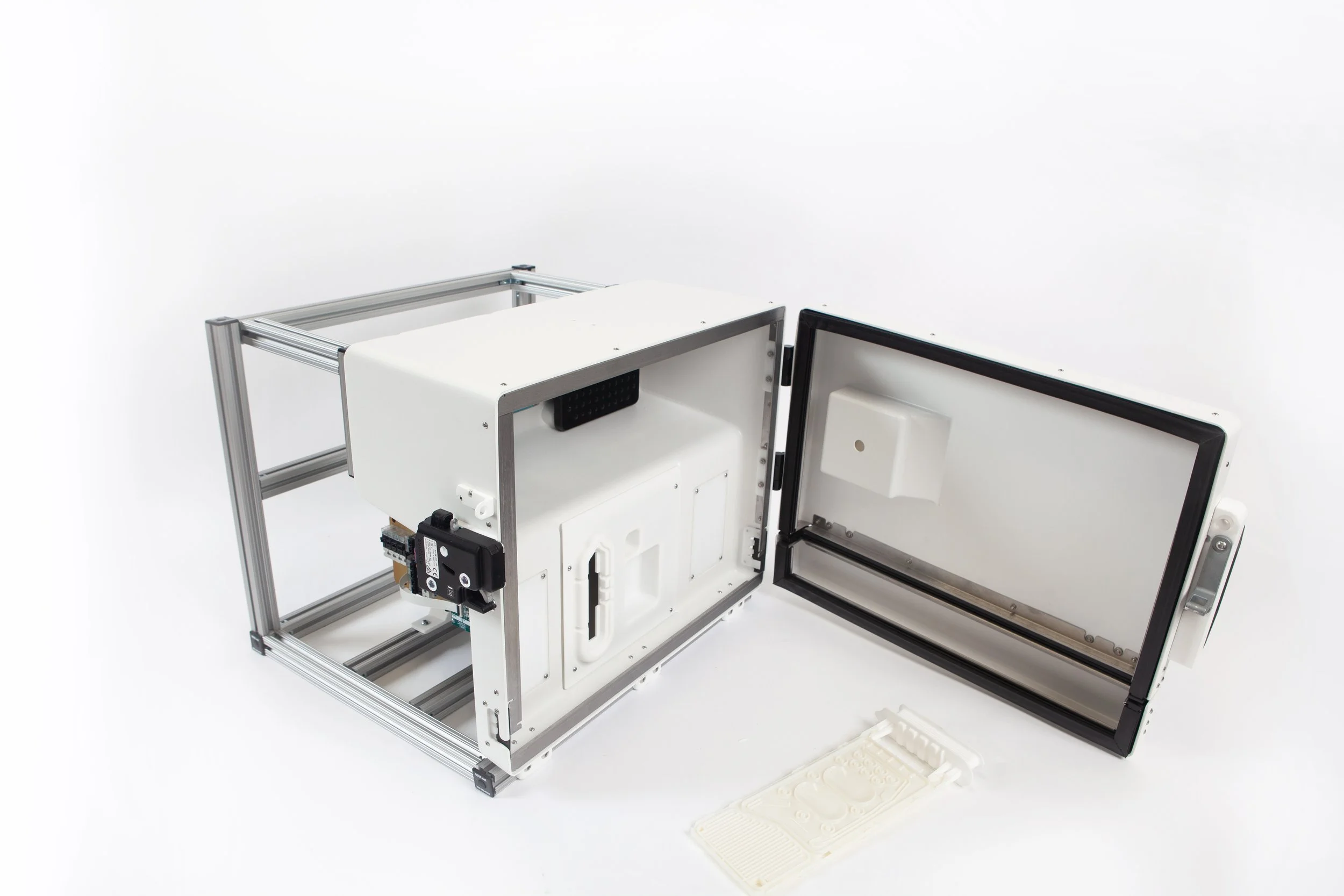
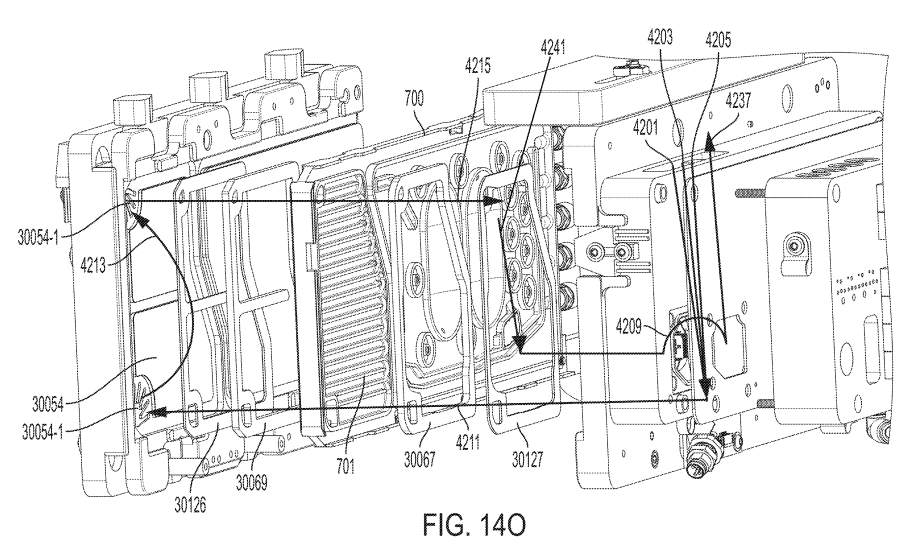
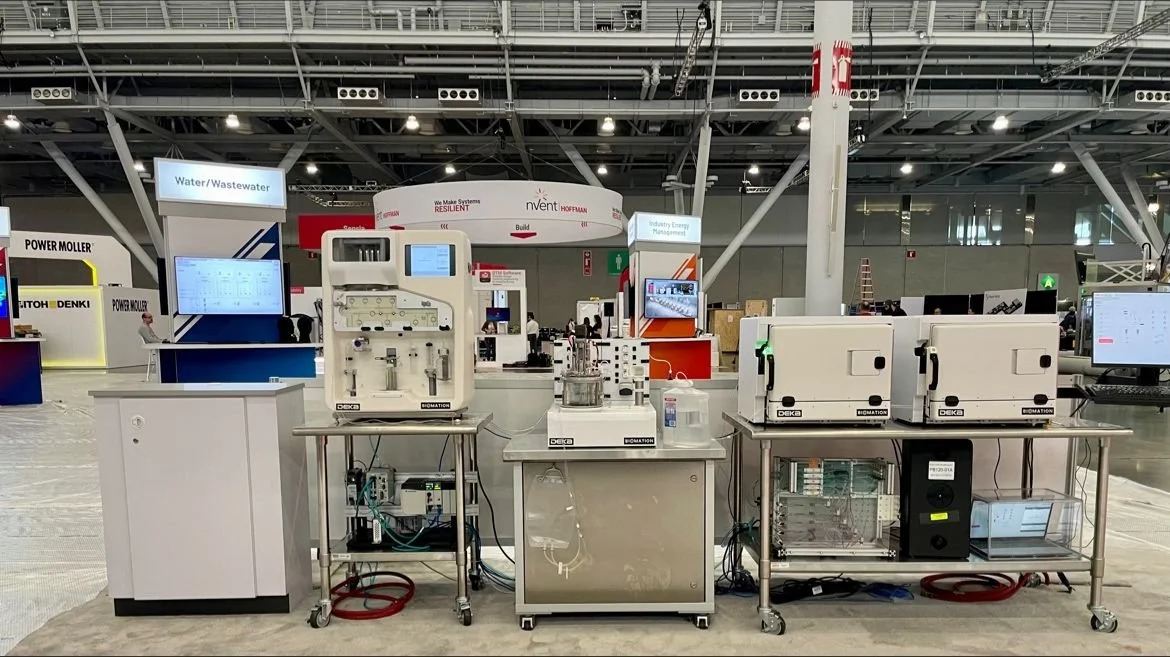

Technical Contributions
Enclosure Design
The cell culturing environment and bioreactors required a thermally isolated, medical grade, cleanroom compatible enclosure. I contributed to the technical design of the enclosure with focus on critical requirements for thermal insulation and environmental sealing. The enclosure was manufactured using cast urethane manufacturing methods, and I oversaw the creation, detailing, and release of technical drawings. As the primary point of contact with the vendor, I was responsible for managing the procurement, manufacturing, and final assembly phases.
Casted polyurethane was selected for its thermal insulation properties and further reinforced with foam insulation. Custom-designed sheet metal brackets were integrated along the internal perimeter of the enclosure to support rubber gaskets, effectively replicating the sealing mechanism of a refrigerator door. The structural integrity of the enclosure was strengthened using an 8020 aluminum frame with custom brackets for additional support.
Disposable Cassette
Assembly & Manufacturing
The fluid management system incorporated a disposable membrane pump cassette and manifold valve configuration. The cassette had a plastic body with molded pump and valve geometry, ultrasonically welded between silicone membranes to control the pumping mechanism and facilitate gas exchange. I contributed to the initial DFM discussions, ensuring the cassette was optimized for injection molding. I also led the manufacturing process, establishing the optimal ultrasonic welding parameters for attaching the membranes to the cassette. In addition, I played a key role in the initial production of over 500 units, developing manufacturing fixtures, assembly aids, and detailed work instructions, while implementing cost-saving measures that reduced both material costs and assembly time.
System Assembly
I led the assembly, integration, and commissioning of 10 complex prototype units, managing all aspects of part procurement, inventory and revision control, and schedule coordination. Each system was pneumatically plumbed in series to the adjacent units, ensuring efficient and reliable airflow throughout the setup along with serviceability. Responsibilities included establishing PLC communication, pneumatic plumbing, electrical wiring, and system debugging for prototypes comprising over 200 unique components, each weighing approximately 60 lbs. These units were built in a controlled bio-laboratory environment and subjected to initial V&V testing, ensuring alignment with product requirement specifications and accumulating thousands of hours of runtime. I collaborated closely with cross-functional teams—controls, biology, systems, and testing—to ensure seamless integration and optimal system performance across all disciplines.
Additional Responsibilities
Fixture Design
Designed and developed multiple assembly aid fixtures to streamline the manufacturing process for both the durable system and disposable units. These fixtures included component alignment for sensors, positioning aids for ultrasonic welding processes, and general tools to enhance operator efficiency.
V&V Testing
Collaborated closely with the test team to develop and execute V&V testing protocols. This involved supporting root cause analysis, performing detailed data analysis, and contributing to the development of next-generation designs based on test findings and system performance evaluations.
Detailed Drawings & Release
Produced detailed technical drawings for over 50 custom parts, ensuring accuracy and manufacturability across various processes, including 3D printing (SLS, SLA, MJF) machining, sheet metal fabrication, cast urethane, and injection molding. These designs were successfully released for manufacturing.
Patent Filing
Worked with the legal team to clearly communicate system design objectives and technical requirements, providing key drawing views to support the patent application process. This collaboration resulted in the successful filing of a patent.
Project Management
Developed project schedule estimates and regularly communicated status updates to upper management. Effectively prioritized tasks to ensure successful project execution across multiple cross-functional departments, including mechanical, manufacturing, controls/electrical, test, clinical, and regulatory teams.
Mentorship
Mentored junior engineers and interns throughout the development process, from concept ideation to final assembly. My goal is to provide meaningful challenges that inspire young engineers, giving them the opportunity to take ownership of their work while offering guidance and support to promote their professional growth.